(1) When the extruded billet is put into the mold, the billet should not be cooled too quickly to avoid plasticity reduction and deformation resistance increase; at the same time, avoid excessive temperature difference between the billet surface and the center layer to prevent the extrusion from being defective due to uneven deformation Or the mold is damaged.
(2) Reduce the temperature difference between the mold and the blank, and avoid the rapid rise of the temperature of the mold surface, which will cause the internal temperature difference of the mold to be too large and generate large internal stress, so as to reduce the risk of damage to the mold when it is working.
The specific method of mold preheating is to install a special resistance preheater on the mold, or use a blowtorch or place a red iron block on the mold for preheating. The preheating temperature depends on the temperature of the extrusion blank.
In addition, in the continuous production process of the mold, due to the long-term contact with the billet that is higher than its own temperature, the temperature of the convex and concave molds continues to rise, and the strength and hardness drop sharply, which affects the life of the mold. At the same time, under the action of high extrusion stress, the mold after the temperature rises is more prone to deformation, which seriously affects the shape and dimensional accuracy of the extruded part. Therefore, in the mold structure, you should consider setting up a cooling device or continuously using manual cooling methods to keep the mold temperature in the range of 150-300°C.
In small batch production, compressed air can be used to cool working parts such as convex and concave molds after each forming, or increase the time interval of warm forging forming.
In large-scale production, special measures should be taken to ensure that the mold temperature is stable within the preheating temperature range. The specific four measures are as follows.
(1) When using a mechanical press for continuous production, the number of strokes per unit time can be adjusted appropriately to ensure that there is sufficient time to cool the mold.
(2) Open holes in the mold to enhance internal cooling. For example, use a pump to drive a lubricant with a pressure of 0.12~0.14 MPa into the pores of the mold for exhalation to cool the convex mold, and blow pressure of 0.4~0.5 MPa into the concave mold. Compressed air to cool the die and ejector.
(3) For spray cooling of the mold, the main consideration is the location where the lubricant cannot flow due to the rapid evaporation of water.
(4) The mold is equipped with a water cooling device.
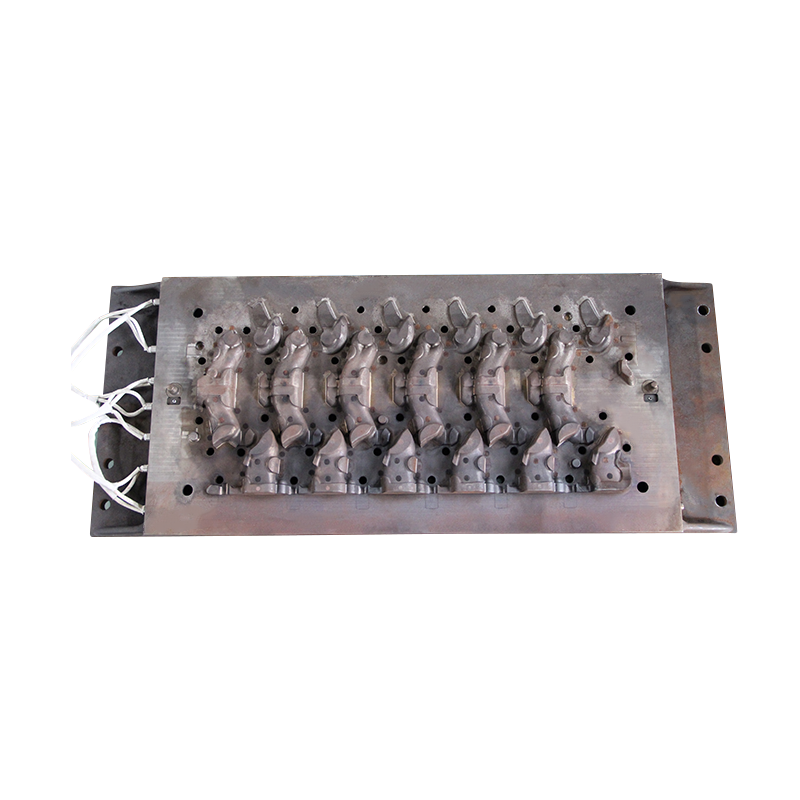