The advantages of fast pouring: the temperature and fluidity of the molten metal are reduced slightly, the cavity is easily filled, and the tendency of subcutaneous pores is reduced. The heat action time on the upper surface of the sand mold during filling is short, which can reduce defects such as sand inclusion. For gray cast iron and nodular cast iron castings, fast casting can make full use of eutectic expansion to eliminate defects such as shrinkage and porosity.
Disadvantages of quick pouring: it has a greater scouring effect on the profile wall, and it is easy to cause defects such as sand expansion and sand washing. The weight of the pouring system is large, and the process yield is low.
The advantage of slow pouring: The scouring effect on the profile wall is small, and it can prevent defects such as sand expansion, box lifting, sand washing and so on. Conducive to the discharge of gas inside the mold. For alloys with larger body shrinkage, when the top pouring method or the inner runner passes through the riser, slow pouring can make the riser smaller, and the gating system consumes less metal.
Disadvantages of slow pouring: during pouring, the molten metal will bake the upper surface of the cavity for a long time, which is easy to produce defects such as sand inclusion and sand sticking. The temperature and fluidity of the molten metal are greatly reduced, and defects such as cold isolation and insufficient pouring are likely to occur. Labor productivity is low.
In recent years, it has been widely recognized that the benefits of fast pouring to castings have been widely recognized, so the pouring time is generally shorter than in the past, especially for gray cast iron and ductile iron.
Calculation of cast iron pouring time:
T=√G+3√G
In the formula, G is the total amount of molten iron in the mold.
In resin sand casting, it is particularly important to increase the pouring speed. According to empirical data, the flow rate must reach at least 150kg/s, and it is required to be faster when pouring grey cast iron and alloy grey cast iron, up to 200kg/s.
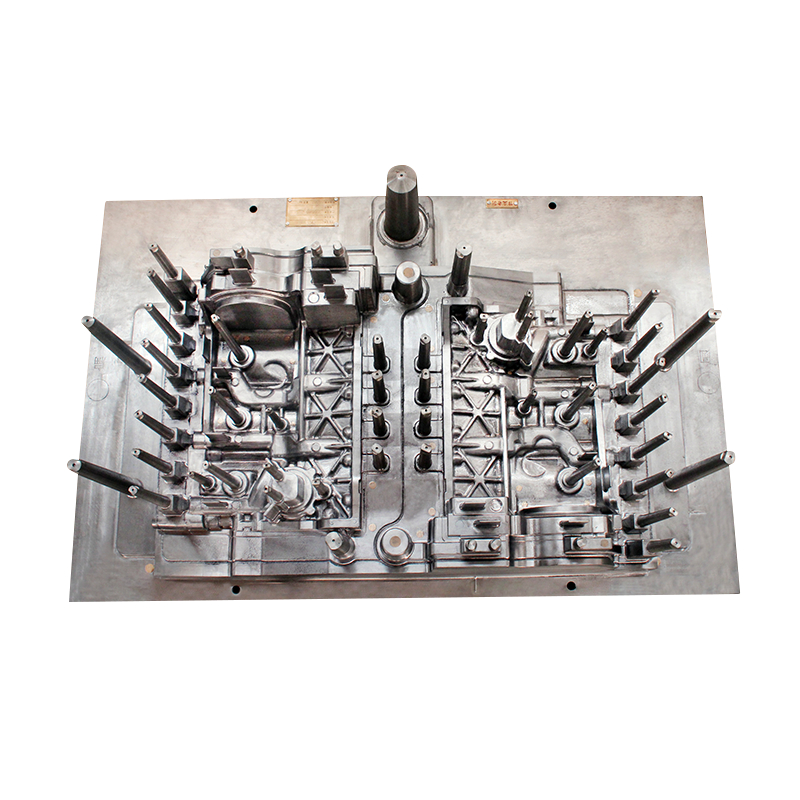