For a visual inspection or flaw detection after dissection, the stomata have a smooth surface and a circular shape.
Causes:
1. The introduction direction of molten aluminum is unreasonable or the flow speed of molten metal is too high, resulting in jetting;
2. Premature blocking of the exhaust duct or frontal impact wall to form a vortex to envelop the air, such pores often produce poor exhaust areas or deep cavities;
3. Because the charge is not clean or the smelting temperature is too high, more gas in the molten metal is not removed, and the precipitation cannot be fully discharged during solidification;
4. The release agent has a large amount of gas or is used too much, and it is not poured before pouring so that the gas is involved in the casting, and the pores are mostly dark gray surface;
5. The high-speed switching point is wrong, the pressure is too low, and the flow opening is too small.
Improvement measures (premise: no flying material during injection)
1. Use clean charge, control smelting temperature, and carry out degassing treatment;
2. Select reasonable process parameters, injection speed, high-speed switching point, energy storage pressure, injection force, flow opening, etc.;
3. Guide the metal liquid balance, fill the cavity in an orderly manner, and facilitate the discharge of gas. It is necessary to improve the runner;
4. The exhaust slot and overflow slot must have sufficient exhaust capacity, and if necessary, increase or enlarge the slag bag and exhaust slot;
5. Select a release agent with a small amount of air and control the air volume.
Shrinkage
1. Anatomical or flaw detection, the cavity is irregular in shape, not smooth, and the surface is dark.
2. Large and concentrated shrinkage pores are small and scattered as shrinkage porosity.
Causes:
1. During the solidification process of the casting, due to shrinkage, the liquid metal cannot be compensated, resulting in cavities;
2. The pouring temperature is too high, and the mold temperature gradient distribution is unreasonable;
3. The injection ratio is low and the boost pressure is too low;
4. The inner gate is thin, the area is too small, and it solidifies prematurely, which is not conducive to pressure transmission and liquid metal feeding;
5. There are hot spots on the casting structure or the cross-sectional area changes drastically;
6. The pouring amount of molten metal is too small, and the remaining material is too thin so that the feeding effect cannot be achieved.
improvement measures
1. Reduce the pouring temperature and reduce the shrinkage;
2. Increase the injection specific pressure and boost pressure to improve the compactness;
3. Modify the inner gate to make the pressure transfer better, which is beneficial to the liquid metal feeding effect;
4. Change the structure of the casting, eliminate the accumulation part of the casting, and make the wall thickness as uniform as possible;
5. Speed up the cooling of thick and large parts;
6. Thicken the handle to increase the feeding effect.
Slag hole
There are metal and non-metallic particles in the die casting that are different from their own materials, and their positions are not fixed. They are not easy to be found during X-ray inspection, and can only be seen on the machined surface.
Causes:
1. Mixing slag:
1) The lining of the melting furnace, transfer package, and holding furnace falls off;
2) After refining in the melting furnace, the slag removal is not complete before the furnace is released;
3) The surface scum is not removed after degassing in the transfer package;
4) When the alloy liquid is poured into the holding furnace, the diversion groove is not clean and not filtered;
5) When pouring, the molten slag on the liquid surface of the holding furnace is not removed and enters the pressure chamber with the pouring spoon.
2. Graphite mixture:
1) The edge of the graphite crucible has fallen off and entered the alloy;
2) Too much graphite in the release agent.
improvement measures
1. Use the following methods to prevent the slag from entering the cavity as much as possible
1) Repair the furnace or replace the furnace lining in time;
2) The melting furnace shall slag to complete and clean in time according to the process requirements;
3) After the transfer bag is degassed, the scum on the surface must be cleaned;
4) To ensure that the diversion groove is clean, a filter device must be installed at the front end;
5) Clean the scum on the liquid surface of the holding furnace. When scooping the alloy liquid with a spoon, scoop it from the liquid surface as much as possible;
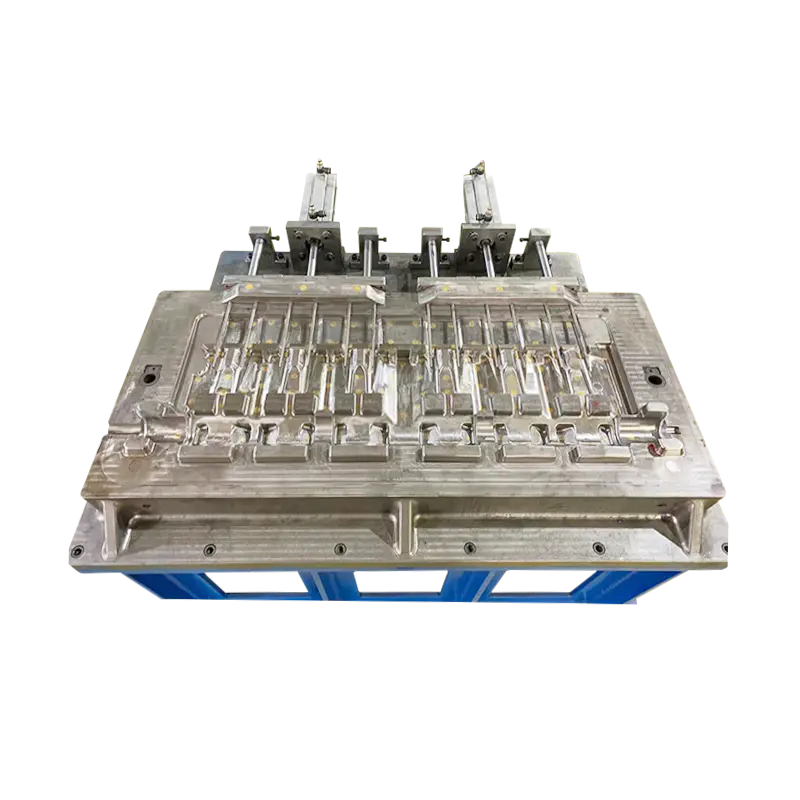