It should be pointed out that in addition to "cavitation", there are other reasons for the "pitting" formed on the surface of aluminum alloy die castings, such as: the surface of the mold is not completely polished after EDM, or the surface of the mold is too bright, This makes the release agent unable to form a good protective film on the surface of the mold, resulting in point-like erosion and mold sticking on the surface of the mold. However, the pits produced by "cavitation erosion" on the surface of the mold are different in shape from such defects, and it is necessary to have enough experience to make a correct judgment.
Causes of Cavitation Erosion in Aluminum Alloy Die Casting
Aluminum alloy die casting is to inject liquid aluminum alloy into the entire cavity of the mold at a high speed by a punch to obtain the desired product. During the flow of molten aluminum, it needs to pass through the runner to reach the inner gate and then spray into the mold cavity. The runner of the mold is the only path for the molten aluminum to flow. The design principle is that the cross-sectional area of the runner should be in a shrinking state, so that the air in the runner can be discharged to the front end of the molten aluminum during the flow of the molten aluminum.
The main reason for cavitation is that the mold design violates the above design principles. On the runner path through which the aluminum alloy liquid flows, the cross-sectional area of the runner expands. When the molten aluminum flows through the expanding inner runner, there will be volume expansion and sudden pressure drop, resulting in the formation of negative pressure (or hollowed out) cavities in the molten aluminum. When the injection is pressurized, the cavity bursts in the runner and inside the mold cavity. When it bursts, it forms an internal explosion, which can generate huge energy. When the product is produced, the continuous multiple implosions cause fatigue deformation on the surface of the metal mold or runner, forming pits that are visible to the naked eye. Correspondingly, protruding pits are formed on the surface of the casting product.
Methods to avoid cavitation in high pressure die casting - correct mold runner design
In the design of the mold runner, the following principles should be followed: the cross-sectional area of the runner from the cake needs to be reduced, and when the runner has branches, the cross-sectional area of the main runner needs to be larger than two or more branch runners The sum of the cross-sectional areas.
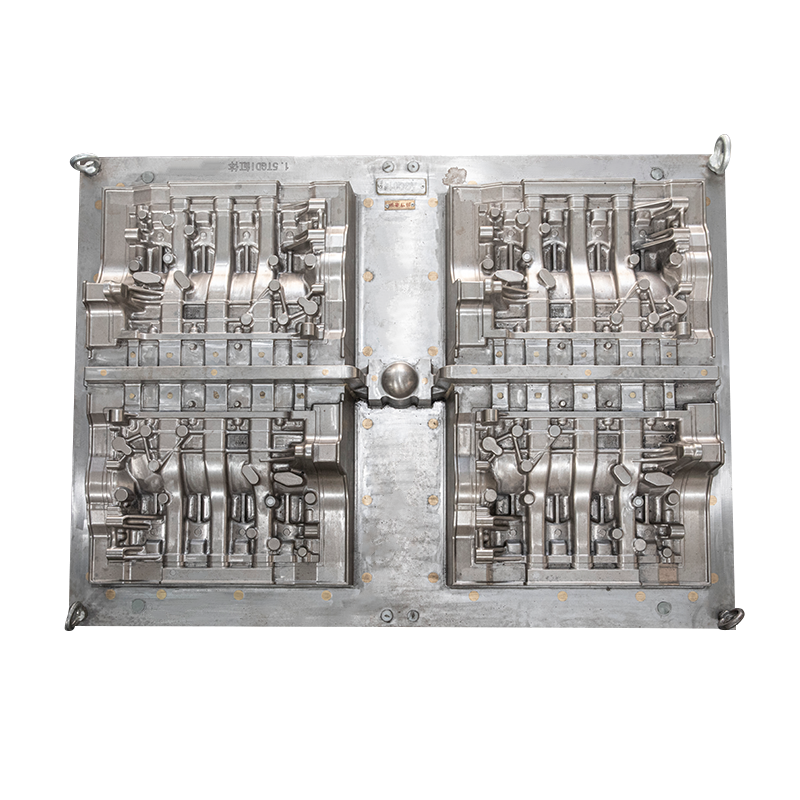